The 7-Second Trick For Alcast Company
The 7-Second Trick For Alcast Company
Blog Article
7 Simple Techniques For Alcast Company
Table of ContentsA Biased View of Alcast CompanyThe Best Strategy To Use For Alcast CompanyNot known Facts About Alcast CompanyThe Basic Principles Of Alcast Company Some Known Facts About Alcast Company.Alcast Company - Truths
Chemical Comparison of Cast Aluminum Alloys Silicon promotes castability by decreasing the alloy's melting temperature and boosting fluidness throughout casting. In addition, silicon adds to the alloy's toughness and put on resistance, making it beneficial in applications where toughness is important, such as vehicle components and engine elements.It additionally boosts the machinability of the alloy, making it less complicated to refine right into ended up products. By doing this, iron adds to the total workability of light weight aluminum alloys. Copper boosts electrical conductivity, making it beneficial in electrical applications. It also enhances deterioration resistance and includes in the alloy's general strength.
Manganese adds to the strength of light weight aluminum alloys and boosts workability (aluminum foundry). It is frequently used in functioned light weight aluminum products like sheets, extrusions, and profiles. The visibility of manganese aids in the alloy's formability and resistance to cracking during construction procedures. Magnesium is a light-weight component that gives toughness and impact resistance to light weight aluminum alloys.
The 8-Minute Rule for Alcast Company
Zinc boosts the castability of aluminum alloys and assists manage the solidification process throughout casting. It improves the alloy's strength and firmness.
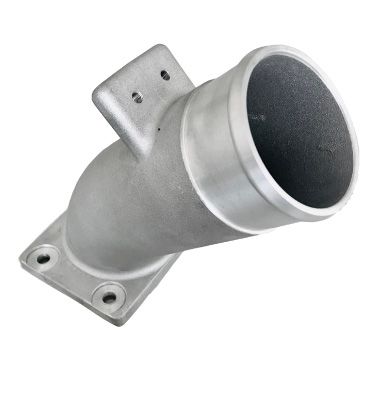
The main thermal conductivity, tensile stamina, return toughness, and prolongation vary. Amongst the above alloys, A356 has the highest thermal conductivity, and A380 and ADC12 have the least expensive.
The Best Guide To Alcast Company

In precision casting, 6063 is fit for applications where elaborate geometries and top quality surface area finishes are vital. Examples include telecommunication rooms, where the alloy's superior formability enables streamlined and aesthetically pleasing designs while maintaining architectural honesty. Similarly, in the Lighting Solutions market, precision-cast 6063 parts create stylish and reliable lighting components that call for detailed forms and excellent thermal performance.
The A360 displays premium elongation, making it optimal for complicated and thin-walled components. In precision casting applications, A360 is well-suited for sectors such as Customer Electronics, Telecommunication, and Power Devices.
All about Alcast Company
Its special properties make A360 a beneficial choice for accuracy casting in these markets, enhancing product resilience and top quality. Aluminum alloy 380, or A380, is a commonly used spreading alloy with numerous distinctive attributes. It offers exceptional castability, making it an ideal option for accuracy casting. A380 displays great fluidness when molten, ensuring detailed and detailed molds are accurately reproduced.
In precision casting, light weight aluminum 413 radiates in the Consumer Electronics and Power Equipment industries. This alloy's premium corrosion resistance makes it an outstanding selection for outside applications, ensuring durable, sturdy items in the discussed industries.
Some Known Details About Alcast Company
When you have actually chosen that the light weight aluminum die casting procedure is ideal for your job, a vital next step is choosing the most suitable alloy. The aluminum alloy you select will considerably impact both the casting process and the residential properties of the last item. Because of this, you should make your decision carefully and take check my site an informed method.
Figuring out the most appropriate light weight aluminum alloy for your application will mean considering a wide array of features. The very first category addresses alloy qualities that affect the production procedure.
4 Easy Facts About Alcast Company Explained
The alloy you pick for die casting straight influences a number of aspects of the spreading procedure, like how very easy the alloy is to deal with and if it is vulnerable to casting flaws. Hot cracking, likewise referred to as solidification cracking, is a regular die casting flaw for aluminum alloys that can cause interior or surface-level rips or fractures.
Specific aluminum alloys are much more at risk to hot breaking than others, and your option should consider this. One more usual defect found in the die casting of aluminum is die soldering, which is when the actors sticks to the die wall surfaces and makes ejection difficult. It can damage both the actors and the die, so you should seek alloys with high anti-soldering properties.
Deterioration resistance, which is currently a significant quality of light weight aluminum, can vary considerably from alloy to alloy and is a crucial particular to think about depending on the environmental problems your item will be exposed to (aluminum foundry). Put on resistance is another home frequently sought in light weight aluminum products and can distinguish some alloys
Report this page